Nickel/Cobalt purification
Cobalt is a brittle, hard transition metal with magnetic properties similar to iron. It is mainly used as an alloy with iron, nickel or other metals to produce corrosion and wear resistant products for high temperature applications (such as jet engines, gas turbines, etc.). Cobalt is normally produced as a by-product of nickel or copper mining.
The purity requirements for Cobalt do not allow nickel to exceed a concentration 0.1%.
Earlier, the nickel was removed by lime precipitations, but as the market specifications became more stringent, ion exchange technologies have been applied.
Base metal impurities normally associated with cobalt include chrome, copper, iron, manganese, nickel and zinc.
Nickel is a hard, silver white metal that has industrial applications related to its strength, corrosion resistance, high ductility, good thermal and electrical conductivity and catalytic properties. Its primary use is in manufacture of stainless steel, steel alloys and superalloys.
The majority of nickel is produced from sulphide sources, this is however changing with production from lateritic sources rising.
In tropical conditions ( warm conditions with abundant rainfall ) nickel laterite can be found in large amounts.
Purifying the nickel and nickel-cobalt separation can be done by ion exchange with IDA and chelating resins.
These resins have a different affinity for the nickel and cobalt and other base metals.
When separating nickel from cobalt, the nickel ion is more strongly retained by the resin. This difference of affinity can be exploited during the elution step of the process by using a split elution. The nickel, which is more strongly retained by the resin, will require a higher eluant concentration than the cobalt.
The purity requirements for Cobalt do not allow nickel to exceed a concentration 0.1%.
Earlier, the nickel was removed by lime precipitations, but as the market specifications became more stringent, ion exchange technologies have been applied.
Base metal impurities normally associated with cobalt include chrome, copper, iron, manganese, nickel and zinc.
Nickel is a hard, silver white metal that has industrial applications related to its strength, corrosion resistance, high ductility, good thermal and electrical conductivity and catalytic properties. Its primary use is in manufacture of stainless steel, steel alloys and superalloys.
The majority of nickel is produced from sulphide sources, this is however changing with production from lateritic sources rising.
In tropical conditions ( warm conditions with abundant rainfall ) nickel laterite can be found in large amounts.
Purifying the nickel and nickel-cobalt separation can be done by ion exchange with IDA and chelating resins.
These resins have a different affinity for the nickel and cobalt and other base metals.
When separating nickel from cobalt, the nickel ion is more strongly retained by the resin. This difference of affinity can be exploited during the elution step of the process by using a split elution. The nickel, which is more strongly retained by the resin, will require a higher eluant concentration than the cobalt.
PuriTech has built up a lot of experience with its ION-IX technology in hydrometallurgy in the last few years.
Adsorption of the nickel and cobalt is done over two or three stages thus providing an increased length to contain the mass transfer zone.
Because the cobalt and the nickel have a different elution zone all metals can be recycled back.
The exact concentrations and volumes required will need to be determined by laboratory / pilot testwork.
After having defined the working conditions a design for a real plant can start.
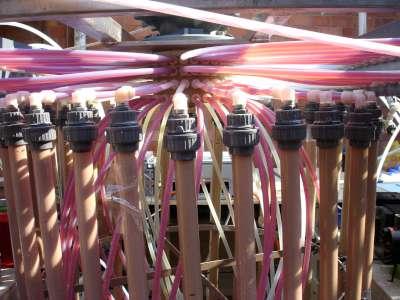
Example of process testing in a pilot.
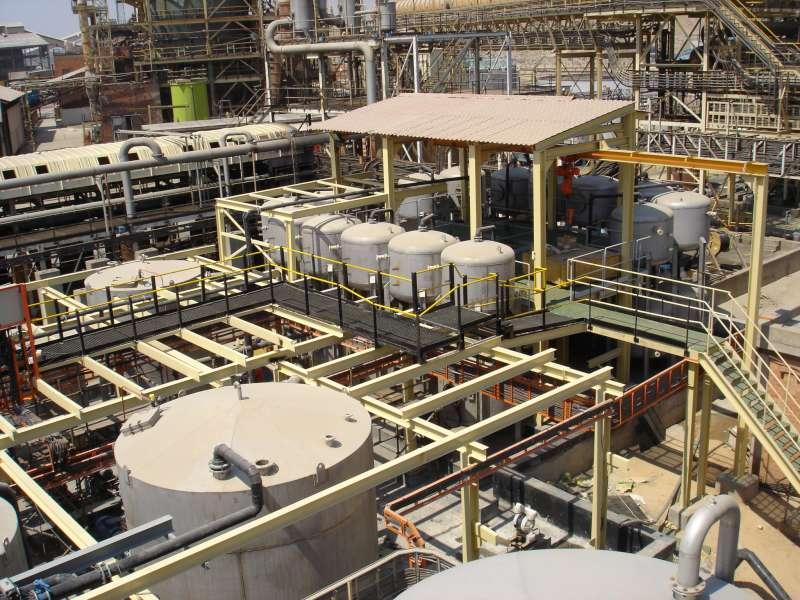